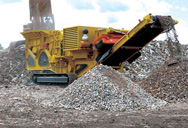
Factors Affecting Ball Mill Grinding Efficiency
ball mill design and efficiency improvement factors. ball mill design and efficiency improvement factors 4.9 - 7499 Ratings ] The Gulin product line, consisting of more than 30 machines, sets the standard for our industry. We plan to help you meet your needs with our equipment, with our distribution and product support system, and the continual introduction and updating of products. Factors ...
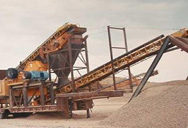
Factors Affecting Ball Mill Grinding Efficiency
a) Mill Geometry and Speed – Bond (1954) observed grinding efficiency to be a function of ball mill diameter, and established empirical relationships for recommended media size and mill speed that take this factor into account. As well, mills with different length to diameter ratios for a given power rating will yield different material retention times, the longer units being utilized for ...
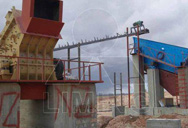
Factors that Impact Efficiency Improvement of …
Factors that Impact Efficiency Improvement of Ball Mill E-mail: [email protected]. What can help you, fill out the form below and submit, we will get back to you as soon as possible. Send a message. Ball mill is one of the most important crushing and grinding machines in the ore dressing plant, but its energy consumption is the highest in the ore beneficiation production line. The working ...
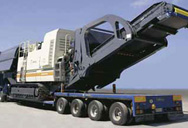
ball mill design and efficiency improvement factors
Ball Mill. Raymond Mill. MW Series Micro Powder Mill. T130X Superfine Grinding Mill. MTW Trapezium Mill. LM Vertical Mill. 5X Pendulum Roller Mill. VSI6X Series Vertical Crusher. Impact Crusher. European Type Jaw Crusher. Jaw Crusher. HPT Hydraulic Cone Crusher. CS Series Cone Crusher. European Impact Crusher . cheapest crushed rock; agglomiration of iron; sahaviriya plate mill; sugar …
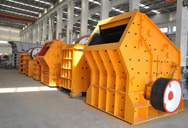
Design Method of Ball Mill by Sumitomo stone Co., Ltd ...
On the other hand, with the recent improvements in Design Method of Ball Mill by Discrete Element Method The grinding rate of gibbsite in tumbling and rocking ball mills using fins was well correlated with the spe- cific impact energy of the balls calculated from Discrete Element Method simulation. This relationship was successfully used for the scale-up of a rocking ball mill, and the optimum ...
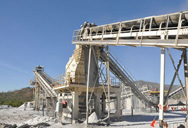
(PDF) DESIGN AND FABRICATION OF MINI BALL …
A numerical dynamic-mechanical model of a planetary ball-mill is developed to study the dependence of process efficiency on milling parameters like ball size and number, jar geometry and velocity ...
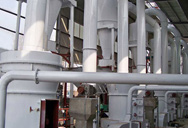
Optimization of mill performance by using
Optimization of mill performance by using online ball and pulp measurements In the platinum industry, by increasing the solid content in the slurry, the product becomes finer. At a higher percentage solid than 73 to 74%, the product becomes coarser again. At this level, a drop in grinding efficiency occurs. (Figure 7.)
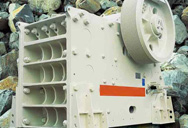
Ball Mill Design/Power Calculation
The basic parameters used in ball mill design (power calculations), rod mill or any tumbling mill sizing are; material to be ground, characteristics, Bond Work Index, bulk density, specific density, desired mill tonnage capacity DTPH, operating % solids or pulp density, feed size as F80 and maximum ‘chunk size’, product size as P80 and maximum and finally the type of circuit open/closed ...
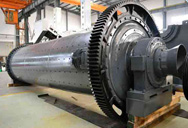
How to Size a Ball Mill -Design Calculator & …
2) Ball milling – a ball mill with a diameter of 2.44 meters, inside new liners, grinding wet in open circuit. When the grinding conditions differ from these specified conditions, efficiency factors (Rowland and Kjos, 1978) have to be used in conjunction with equation 1. In general, therefore, the required mill power is calculated using the ...
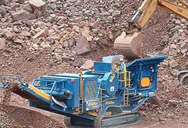
CALCULATION OF BALL MILL GRINDING …
08.03.2013 · calculation of ball mill grinding efficiency. dear experts . please tell me how to calculate the grinding efficiency of a closed ckt & open ckt ball mill. in literatures it is written that the grinding efficiency of ball mill is very less [less than 10%]. please expalin in a n excel sheet to calcualte the same. thanks. sidhant. reply
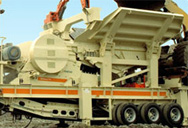
How to Measure Grinding Efficiency
The first two Grinding Efficiency Measurement examples are given to show how to calculate Wio and Wioc for single stage ball mills. Figure 1. The first example is a comparison of two parallel mills from a daily operating report. Mill size 5.03m x 6.1m (16.5′ x 20′ with a ID of 16′). This example shows that Mill 2 is slightly more efficient than Mill 1 even though it has a higher power ...
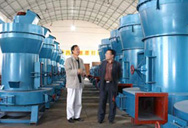
Factors That Affect Ball Mill Grinder Capacity And …
Factors That Affect Ball Mill Grinder Capacity And Quality 7 factors that affect the output of ball mill machine The stone size of raw material. Since the vertical kiln cement plant uses the small ball mill, the stone size of raw material can greatly affect its capacity and quality. The smaller the particle size, the higher the yield and quality of the ball mill. On the contrary, the larger ...
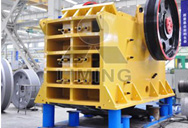
Ball mill - Wikipedia
A ball mill is a type of grinder used to grind, blend and sometimes for mixing of materials for use in mineral dressing processes, paints, pyrotechnics, ceramics and selective laser sintering.It works on the principle of impact and attrition: size reduction is done by impact as the balls drop from near the top of the shell. A ball mill consists of a hollow cylindrical shell rotati

Ball Mills - Mineral Processing & Metallurgy
This is the most economical design and thus lowest in first cost. Mill can not be converted into longer mill at a later date. Grinding Mill TYPE B Built with shell double welded into one of the steel heads and with the other edge double welded to steel flange which is bolted to the other steel head. While first cost is higher it can be later converted. Grinding (Rod) or (Ball) Mill TYPE C Has ...

THE OPTIMAL BALL DIAMETER IN A MILL
efficiency, as well as its confirmation by the results of the experimental explorations. keywords: mineral processing, optimal ball diameter, optimal ball charge, grinding 1. Introduction The ball size in a mill has a significant influence on the mill throughput, power consumption and ground material size (Austin et al., 1976; Fuerstenau et al., 1999; Kotake et. al., 2004). The basic condition ...
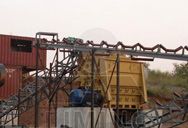
Factors Affecting the Efficiency of Ball Mill Essay - …
Ball mill is widely used in refractory plant, cement plant, glass plant and metallurgy plant etc.,ball mill adopts roll bearing,its energy saving is reduced 30% than the overflow ordinary ball mill, low noise and high output efficiency make ball mill environmental protection,Great Wall company introduces the overall ball mill frame,it is convenient to install and transport. 1.Pre-sales Service ...
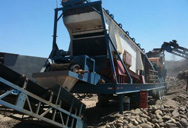
The energy efficiency of ball milling in …
Schoenert (1986) proposed several different definitions for the energy efficiency of ball mills, depending on the type of reference chosen. The first is what he termed the theoretical efficiency, which is based on fracture physics data for the material. According to this definition, given that the energy utilization in a ball mill is between 1×10 −3 and 4×10 −3 m 2 /J, and that the crack ...
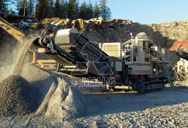
Grinding in Ball Mills: Modeling and Process Control
The design of a ball mill can vary significantly depending on the size, the equipment used to load the starting material (feeders), and the system for discharging the output product. The size of a mill is usually characterized by the ratio “length to diameter” and this ratio most frequently varies from 0.5 to 3.5. The starting material can be loaded either through a spout feeder or by ...