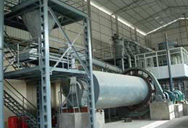
How Ball Mills Work (Engineering and Mining) - …
20-6-2019 · For both wet and dry ball mills, the ball mill is charged to approximately 33% with balls (range 30-45%). Pulp (crushed ore and water) fills another 15% of the drum’s volume so that the total ...
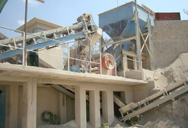
Ball Mills - Metallurgist & Mineral Processing …
13-2-2017 · Working Principle & Operation. The apparent difference in capacities between grinding mills (listed as being the same size) is due to the fact that there is no uniform method of designating the size of a mill, for example: a 5′ x 5′ Ball Mill has a working diameter of 5′ inside the liners and has 20 per cent more capacity than all other ball mills …
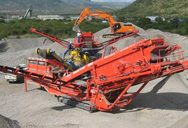
Ball Mills - an overview | ScienceDirect Topics
Ball mills are commonly used for crushing and grinding the materials into an extremely fine form. The ball mill contains a hollow cylindrical shell that rotates about its axis. This cylinder is filled with balls that are made of stainless steel or stone to the material contained in it.
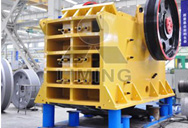
Ball mill - Wikipedia
A ball mill, a type of grinder, is a cylindrical device used in grinding (or mixing) materials like ores, chemicals, ceramic raw materials and paints.Ball mills rotate around a horizontal axis, partially filled with the material to be ground plus the grinding medium. Different materials are used as media, including ceramic balls, flint pebbles and stainless steel balls.
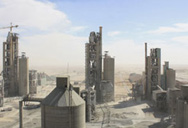
Ball Milling Method - YouTube
1-4-2016 · How Ball Mills Work (Engineering and Mining) - Duration: 15:30. saVRee 3D 29,430 views. ... Prototype high energy eliptical ball mill for nanopowder metallurgy - Duration: 1:16. Gray Scot 7,769 ...
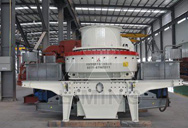
Mill Process Engineering Solutions - …
MPES provides engineering services in mineral processing. Particularly, for grinding and flotation. MPES experts of grinding (HPGR, SAG/AG, Ball Mill grinding) and flotation offer expertise level detailed mill and flotation solutions. Flowsheet design and optimization, Population Balance Modeling, Discrete Element Modeling are the main areas on which MPES feels so strong in all over the world.
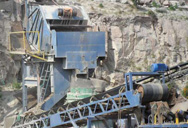
Understanding Ball Mill Sizing | Industrial & …
Effect of ball size and powder loading on the milling efficiency of a laboratory-scale wet ball mill. Ceramics International 2013, 39 (8) , 8963-8968. DOI: 10.1016/j.ceramint.2013.04.093. Vedat Denız. Computer Simulation of Product Size Distribution of a Laboratory Ball Mill.
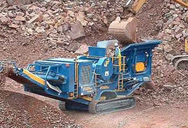
ACCS Ltd - Ball Mill Relining
Case Studies : Ball Mill Relining . Ball milling is a primary method of grinding coarse materials to a fine powder. Typically employed in the ceramics, metallurgical, paint and glass industries, ball milling uses abrasive grinding media (such as ceramic balls, flint pebbles or …
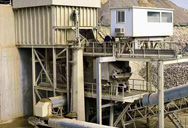
High-Energy Ball Milling - an overview | …
High-energy ball milling is a ball milling process in which a powder mixture placed in a ball mill is subjected to high-energy collisions from the balls. High-energy ball milling, also called mechanical alloying, can successfully produce fine, uniform dispersions of oxide particles in nickel-base super alloys that cannot be made by conventional powder metallurgy methods.
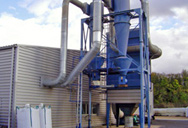
Ball Mill - Ball Grinding Mill ... - Raymer Engineering
Raymer Engineering is one of the leading manufacturers, supplier and exporter of Ball Mills in Mumbai, India.Our Ball Mills complies with international standards. In this product range, we also offer shrouded ball mills that are extensively used in various industrial sectors for dispersion of enamels & primers, powder distempers and cement paints.
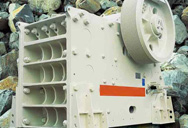
Ball Mill Design/Power Calculation
The basic parameters used in ball mill design (power calculations), rod mill or any tumbling mill sizing are; material to be ground, characteristics, Bond Work Index, bulk density, specific density, desired mill tonnage capacity DTPH, operating % solids or pulp density, feed size as F80 and maximum ‘chunk size’, product size as P80 and maximum and finally the type of circuit open/closed ...
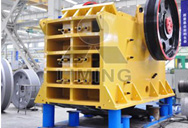
Chem Soc Rev - ResearchGate
Chem.Soc.Rev. his ournal is c he Royal Society of Chemistry 2013 fromhighaccelerations.1 Otherbenefitsin comparison toother ball mill types like mixer mills or stirred media mills …
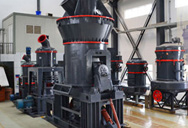
Process engineering with planetary ball mills - …
Planetary ball mills are well known and used for particle size reduction on laboratory and pilot scales for decades while during the last few years the application of planetary ball mills has extended to mechanochemical approaches. Processes inside planetary ball mills are complex and strongly depend on the processed material and synthesis and, thus, the optimum milling conditions have to be ...
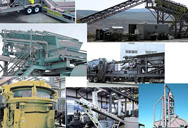
Milling (machining) - Wikipedia
Milling is the process of machining using rotary cutters to remove material by advancing a cutter into a work piece. This may be done varying direction on one or several axes, cutter head speed, and pressure. Milling covers a wide variety of different operations and machines, on scales from small individual parts to large, heavy-duty gang milling operations.
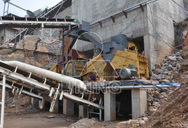
Ball Mill - RETSCH - powerful grinding and …
RETSCH is the world leading manufacturer of laboratory ball mills and offers the perfect product for each application. The High Energy Ball Mill E max and MM 500 were developed for grinding with the highest energy input. The innovative design of both, the mills and the grinding jars, allows for continuous grinding down to the nano range in the shortest amount of time - with only minor warming ...
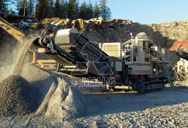
Quadro Engineering - Powder Milling and Particle …
Quadro Engineering, a division of IDEX MPT, Inc has earned the respect & trust of customers worldwide through our commitment to improving the performance of their powder processing operations. We set the standards by which others are measured.
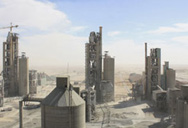
Process engineering with planetary ball mills.
21-9-2013 · Process engineering with planetary ball mills. Burmeister CF(1), Kwade A. Author information: (1)Technische Universität Braunschweig, Institute for Particle Technology, Volkmaroder Straße 5, 38104 Braunschweig, Germany. [email protected] [email protected].
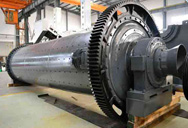
Ball Mills - Mine Engineer.Com
Ball Mills are generally used to grind material 1/4 inch and finer, down to the particle size of 20 to 75 microns. To achieve a reasonable efficiency with ball mills, they must be operated in a closed system, with oversize material continuously being recirculated back into the mill to be reduced.
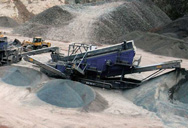
What Is a Ball Mill? - Monroe Engineering
It’s called a “ball mill” because it’s literally filled with balls. Materials are added to the ball mill, at which point the balls knock around inside the mill. How a Ball Mill Works. Ball mills work by using balls to grind materials. Materials such as iron ore, pain and ceramics are added to the ball mill. Next, the ball mill …
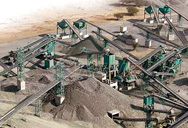
Grinding in Ball Mills: Modeling and Process Control
Keywords: Ball mills, grinding circuit, process control. I. Introduction Grinding in ball mills is an important technological process applied to reduce the size of particles which may have different nature and a wide diversity of physical, mechanical and stone characteristics. Typical examples are the various ores, minerals, limestone, etc.