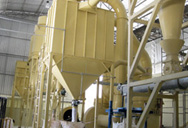
New dry iron ore processing technology …
New Steel CEO Gustavo Emina said, “Before the invention, the only technology available to raise the content of very fine iron ore particles was flotation, but flotation is water-sensitive and is ...
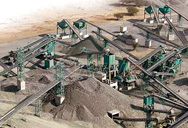
Iron Ore Processing Plants - Iron Ore Wash Plants …
Iron Ore. Efficiently remove silica and alumina contamination to increase efficiencies in steel production. Our iron ore wet processing plants are proven to successfully deal with silica and alumina contamination in the iron ore, resulting in an increase in the Fe value of the iron ore thereby increasing the efficiency of the steel production process.
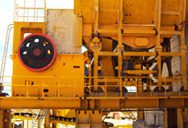
fine form iron ore agglomerate when they are wet
Hematite Iron Ore Beneficiation Plant: , wet screen technology iron fines; wet iron ore sinter concentrate; do fine form iron ore agglomerate when they are wet; Iron Ore | HowStuffWorks. The majority of Earths iron, however, exists in iron ore Mined right out of the ground, raw ore is mix of ore proper and loose earth called gangue The ore proper can usually be separated by crushing the raw ...
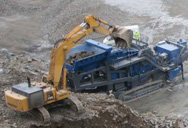
Iron ore – improving ore quality - AusIMM Bulletin
Some iron ore companies are already marketing ‘green’ iron ore pellets, while others are only just starting to develop beneficiation processes for their production sites. For a high-grade iron ore deposit (ie greater than 62 per cent), a dry crushing and sizing process is sufficient to achieve the required product quality and size fraction as lump ore, sponge ore or sinter fines (MetalBulletin, 2014).
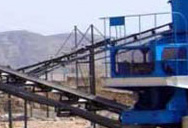
iron fines wet grindig process - arcimarche.it
iron fines wet grindig process HFC Refrigerants (55) HST Hydraulic Cone CrusherHST series hydraulic cone crusher is combined with technology such as machinery, hydraulic pressure, electricity, automation, intelligent control, etc. , representing the most advanced crusher technology in the world.
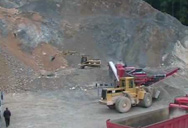
The Latest Developments in Iron Ore Processing
Introduction: Iron Ore Processing. Largest Iron Suppliers • Vale • BHP • Rio Tinto • Kumba Iron ore Overview. Iron Ore Sources • Hematite (Fe2O3) • Magnetite (Fe3O4) • TitaniferousMagnetite (Fe2+ (Fe3+,Ti) 2O4) Overview. Occurrence • Massive • Banded Iron Formation (BIF) • Limonite • Taconite Overview • Main Use of Iron Ore –Steel Industry • Iron Ore Processing in ...
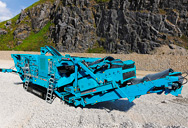
Iron Ore Processing for the Blast Furnace
Iron Ore Processing for the Blast Furnace (Courtesy of the National Steel Pellet Company) The following describes operations at the National Steel Pellet Company, an iron ore mining and processing facility located on the Mesabi Iron Range of Minnesota. Creating steel from low-grade iron ore requires a long process of mining, crushing, separating, concentrating, mixing, pelletizing, and ...
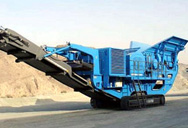
Case Study: Paste thickening optimises tailings …
After primary and secondary crushing, the processing of Khumani’s iron ore involves wet washing and screening, jigging and fines recovery through the use of de-grit cyclones. Because each of ...
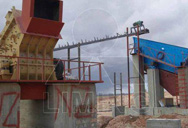
The case for wet processing iron ore - HAVER …
Many iron ore producers are facing challenging times; processing crude material with rising levels of impurities and a volatile iron ore price. Beneficiation, particularly washing (scrubbing), can be the key to upgrading the ore to earn more per shipped tonne. High-end steel production at a low coke consumption level and a high productivity rate can only be achieved by using high-quality ...
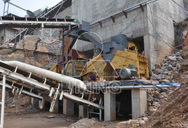
CHAPTER-10 DE-WATERING OF IRON ORE FINE PARTICLES IN ...
During the wet processing of iron ores, a considerable amount of fine particles, known as slimes, are generated which need to be recovered effectively through solid -liquid separation. This assumes even more importance in case of iron ores in view of the large tonnage treated in India or elsewhere in the world. Proper de-watering is essential due to : (a) Material recovery : Slimes to the tune ...
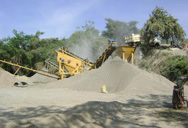
Processing of Goethitic Iron Ore Fines | SpringerLink
09.05.2015 · In the present investigation an attempt has been made to beneficiate goethitic iron ore containing 59.02 % Iron, 6.51 % Alumina, 4.79 % Silica, 0.089 % Phosphorus with 7.11 % loss on ignition. For this purpose, different beneficiation techniques such as gravity and magnetic separation processes have been employed. During the process two conceptual flow sheets were also developed …
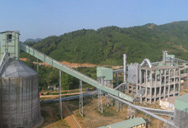
Iron ore wet processing plants, CDE Asia
Our iron ore processing plants target these contaminants and ensure their effective removal from the feed to the kilns. This has the effect of increasing the Fe value of the iron ore allowing for a more efficient steel production process.
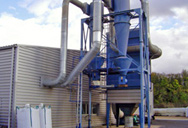
Sampling and testing iron ore fines – Aide-mémoire
For iron ore fines (IOF) this includes: Cargo group (i.e. Group A – cargoes which may liquefy), Total quantity of cargo to be offered Stowage factor Need for trimming and trimming procedures Certificate of moisture content (MC) and its transportable moisture limit (TML) Likelihood of formation of a wet …
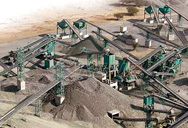
Dry screening iron ore - YouTube
07.09.2016 · As an universal practice, iron ore is dislodged by drilling blast holes according to dry screening of iron ore fines - crusher machine dry screening of iron ore fines. This page is provide ...
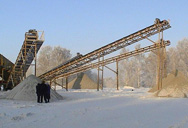
(PDF) Processing of Magnetite Iron …
Currently unmined, hematite quartzites are the feedstock for Krivoi Rog MPIW and for future preparation plants of various MPIWs and mines in the Krivoi Rog Iron Ore Basin. In view of fine ...
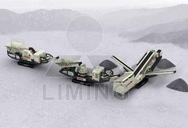
what is a wet processing plant iron ore - LinkedIn …
Innovative Iron Ore Processing Systems for Flagship Bellzone Project iron ore assets in Guinea, West Africa: Forecariah ... this plant have lower iron content which adversely ... chosen to develop a tailored iron ore wet processing. Iron Ore Processing for the Blast Furnace Creating steel from low-grade iron ore requires a long process of mining, crushing, separating ... National Steel Pellet ...
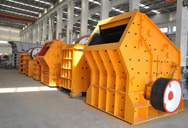
Processing plant | Roy Hill
Processing plant. The processing plant consists of six individual scrubbing, screening and de-sanding circuits. The wet scrubbing units are used to break down the sticky clays attached to the ore, into a fine suspended clay fraction suitable for subsequent wet beneficiation. Beneficiation is the process of separating the valuable material from the