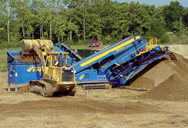
How to Improve Ball Mill Performance
Ball mill circuit classification system performance is considered here first because it provides the basis for subsequent characterization of ball mill breakage efficiency. Major design and operating variables in closed circuit ball milling of a specified feed to a desired product size are summarized in Table 1.
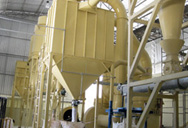
MODULE #5: FUNCTIONAL PERFOMANCE OF BALL MILLING
the functional performance equation for ball milling: Circuit Ball mill Classification Ore Ball mill output = power x system x grindability x grinding
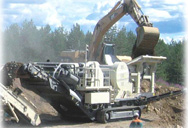
Factors Affecting Ball Mill Grinding Efficiency
b) Feed Preparation – With more widespread use of coarse ball milling it is increasingly important to present a suitable feed material top-size to the ball mill. Significant inefficiencies are introduced as a result of the need for larger (and, as a result, fewer) grinding balls. Furthermore, as mill performance is related to the complete size distribution of the feed material, all ...
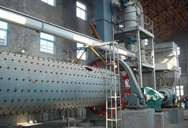
Sulfur–Graphene Nanostructured Cathodes via Ball …
Although much progress has been made to develop high-performance lithium–sulfur batteries (LSBs), the reported physical or stone routes to sulfur cathode materials are often multistep/complex and even involve environmentally hazardous reagents, and hence are infeasible for mass production. Here, we report a simple ball-milling technique to combine both the physical and stone routes ...
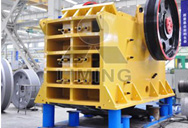
Ball mill - Wikipedia
A ball mill, a type of grinder, is a cylindrical device used in grinding (or mixing) materials like ores, chemicals, ceramic raw materials and paints.Ball mills rotate around a horizontal axis, partially filled with the material to be ground plus the grinding medium. Different materials are used as media, including ceramic balls, flint pebbles and stainless steel balls.
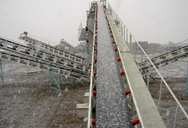
Ball Milling - an overview | ScienceDirect Topics
Ball milling technique, using mechanical alloying and mechanical milling approaches were proposed to the word wide in the 8th decade of the last century for preparing a wide spectrum of powder materials and their alloys. In fact, ball milling process is not new and dates back to more than 150 years. It has been used in size comminutions of ore, mineral dressing, preparing talc powders and many ...
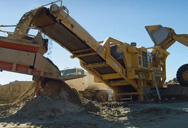
EFFECTS OF GRINDING MEDIA SHAPES ON BALL MILL …
EFFECTS OF GRINDING MEDIA SHAPES ON BALL MILL PERFORMANCE Niyoshaka Nistlaba Stanley Lameck A dissertation submitted to the Faculty of Engineering and The Built Environment, University of the Witwatersrand, Johannesburg, in fulfilment of the requirements for the degree of Master of Science in Engineering Johannesburg, October 2005
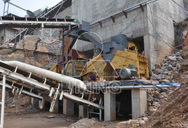
Ball Mill - RETSCH - powerful grinding and …
RETSCH is the world leading manufacturer of laboratory ball mills and offers the perfect product for each application. The High Energy Ball Mill E max and MM 500 were developed for grinding with the highest energy input. The innovative design of both, the mills and the grinding jars, allows for continuous grinding down to the nano range in the shortest amount of time - with only minor warming ...
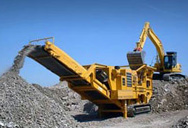
Functional Performance Analysis Of Ball Milling
Performance Evaluation Of Ball Mill Liverpoolturismo.It. Module 5 functional perfomance of ball milling in this module, you will learn how to characterize the performance of ball mill circuits. specifically, after completing this module, you will be able to list and describe the four elements of the functional performance equation for ball mill circuits.
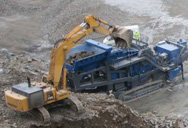
THE EFFECTS OF HIGH ENERGY MILLING ON THE PERFORMANCE …
Milling reduced particle size, enhanced amorphism, and increased the release of structural cations from the rocks, with the effects due to dry milling being greater than for wet milling. The optimum milling times which produced maximum amounts of exchangeable cations (Na, K, Ca, and Mg) were 30 - 90 min, depending on rock type.
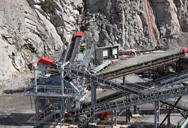
The effect of ball size on mill performance - …
The specific rates of breakage of particles in a tumbling ball mill are described by the equation S i = ax α i (Q(z), where Q(z) is the probability function which ranges from 1 to 0 as particle size increases.This equation produces a maximum in S, and the particle size of the maximum is related to ball diameter by x m = k 1 d 2.The variation of a with ball diameter was found to be of the form ...
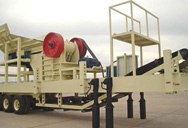
Optimization of mill performance by using
Optimization of mill performance by using online ball and pulp measurements Soon after a stop, a mill is a dangerous place to enter for the personnel tasked with taking measurements or samples. Crash stops are difficult to handle. The mill and all feed streams should be stopped simultaneously but, often, they are stopped around about the same time.
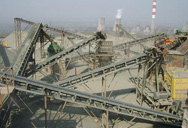
Ball Mill: Operating principles, components, Uses ...
Several types of ball mill exist. They differ to an extent in their operating principle. They also differ in their maximum capacity of the milling vessel, ranging from 0.010 litres for planetary ball mill, mixer mill or vibration ball mill to several 100 litres for horizontal rolling ball mills.
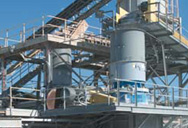
189 questions with answers in BALL MILLING | …
25-3-2020 · Dear All, I am facing a problem during ball milling that the Pure aluminum with 15 % Alumina by volume reinforcement is becoming reactive in open air after 24 hours of ball milling.
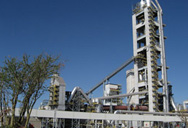
New Tyhigh Performance Gold Ore Ball Milling - …
How to Improve Ball Mill Performance. Ball mill circuit classification system performance is considered here first because it provides the basis for subsequent characterization of ball mill breakage efficiency Major design and operating variables in closed circuit ball milling of a specified feed to a desired product size are summarized in Table 1
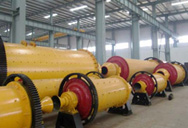
Si@SiOx/Graphene Nanosheets Composite: Ball …
Si@SiOx/grapheme nanosheet (Si@SiOx/GNS) nanocomposites as high-performance anode materials for lithium-ion batteries are prepared by mechanically blending the mixture of expanded graphite (EG) with Si nanoparticles, and characterized by Raman spectrum, X-ray diffraction (XRD), field emission scanning electron microscopy, and transmission electron microscopy. During ball milling process, the ...
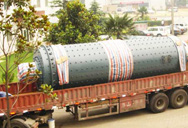
Variables in Ball Mill Operation | Paul O. Abbe®
Ball mill operation is often regarded as something of a mystery for several reasons. Ball milling is not an art - it’s just physics. The first problem will ball mills is that we cannot see what is occurring in the mill. The other problem is that many of the independent variables …
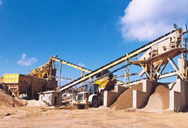
Effect of gallium doping and ball milling ... - …
24-7-2012 · Effect of gallium doping and ball milling process on the thermoelectric performance of n-type ZnO - Volume 27 Issue 17 - Priyanka Jood, Germanas Peleckis, Xiaolin Wang, Shi Xue Dou
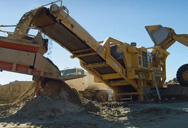
Mechanically exfoliated g-C3N4 thin nanosheets …
g-C 3 N 4 with a layered structure has been proven as an outstanding metal-free organic photocatalyst because of its appropriate bandgap, abundant building elements, and excellent stone stability. Here, a simple one-step ball milling method is presented for synthesis of mechanically exfoliated g-C 3 N 4 (MECN) thin nanosheets at large scales for the first time.
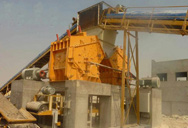
HPC milling cutters - High performance cutting by …
Shop our HPC milling cutters from the Gühring online shop - fast, simple and economic. Convince yourself of the quality made in Germany. We will be happy to advise and support you!